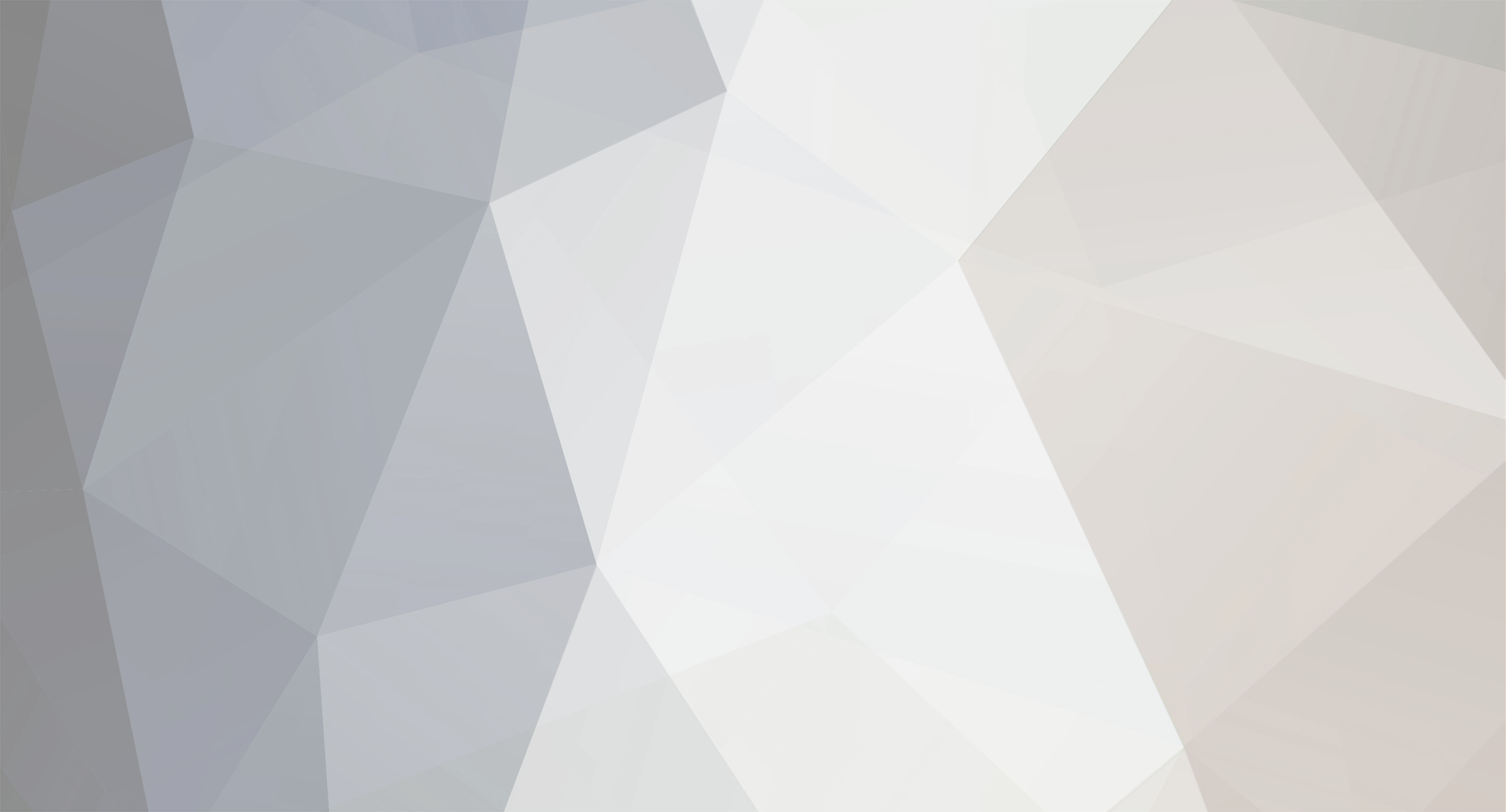
Captain Bondo
Members-
Posts
638 -
Joined
-
Last visited
-
Days Won
2
Content Type
Profiles
Forums
Gallery
Blogs
Downloads
Events
Store
Bug Tracker
Everything posted by Captain Bondo
-
Hussein's 1998 V70 Xr : The Force Awakens
Captain Bondo replied to lookforjoe's topic in Performance Modifications
I just put a tdc mark on the front pulley and front tbelt cover (paint marker). -
Hussein's 1998 V70 Xr : The Force Awakens
Captain Bondo replied to lookforjoe's topic in Performance Modifications
1) Get old sparkplug wire 2) Cut the boot off that attached to the distributor 3) Remove cop. 4) Jam cut off end of old plug wire into the cop 5) Attach other end of plug wire to spark plug 6) Use timing light on plug wire as normal. -
Hussein's 1998 V70 Xr : The Force Awakens
Captain Bondo replied to lookforjoe's topic in Performance Modifications
What brand are the valves? I have federal mogul, they were cheap and seem good. I would definitely replace that guide. -
Hussein's 1998 V70 Xr : The Force Awakens
Captain Bondo replied to lookforjoe's topic in Performance Modifications
No I mean did you physically check the timing with a light to make sure the actual timing agrees with the logs. The logs don't know what the ACTUAL timing is. Sounds like you cured those issues, but it'd be worth verifying this at some point. Bummer dude. Did you check valve clearance using clay this time? If so, what was it like? -
Hussein's 1998 V70 Xr : The Force Awakens
Captain Bondo replied to lookforjoe's topic in Performance Modifications
Does the spark timing itself seem correct? -
Hussein's 1998 V70 Xr : The Force Awakens
Captain Bondo replied to lookforjoe's topic in Performance Modifications
It seems there are quite a few assumptions being made in terms of cam timing, how the lash is being set, how much the head has been cut, etc. I would definitely do a "clay test" as mentioned earlier in the thread when you reassemble it. Really, that's all you can do at this point. Do the test with the intake cam fully advanced and the exhaust cam fully retarded, and just see what you get. -
Hussein's 1998 V70 Xr : The Force Awakens
Captain Bondo replied to lookforjoe's topic in Performance Modifications
My guess would be the cam gear spun on the cam. Youll be able to tell if it's still timed right. But who knows, no point in speculating via the internet. The seats will be fine- if anything in addition to the valves is damaged, it will be the guides. I have seen guides crack from bent valves on whiteblocks. You are assuming the pistons are fine... I have my doubts... I would be at least pulling the worst one to confirm side clearance on the top compression ring. ring side clearance is critical and the crown has taken a pretty hard hit. If it has deformed the ring groove at all you are humped. Also, no way valve float is gonna put huge dents in the pistons like that. The valves got RAMMED into the piston. Are these solid lifter cams (I assume so since the are VVT?)? Obvious question, but - valve lash was correct? -
Hussein's 1998 V70 Xr : The Force Awakens
Captain Bondo replied to lookforjoe's topic in Performance Modifications
The cam retard if it slips on the gear. Retarding the intake cam INCREASES piston to valve clearance. The bolts slipping are not what caused the piston to valve contact. It is likely the other way around, the piston to valve contact caused the bolts to slip. -
Hussein's 1998 V70 Xr : The Force Awakens
Captain Bondo replied to lookforjoe's topic in Performance Modifications
You use the sleeve retainer on the surfaces of the existing press fit and then drill a blind hole through the collar and into the cam and install the roll pin. The slot isn't really subject to any load in normal operation. In what sense would this be unreliable? I know the temptation is to demand justice out of principle, but sometimes you need to just be resourceful, use your head, and git'r'done. -
Hussein's 1998 V70 Xr : The Force Awakens
Captain Bondo replied to lookforjoe's topic in Performance Modifications
Sounds like some sleeve retainer, a roll pin, and about 15 minutes of work and you'd be back in business. I would avoid welding it. Still, what a pita though man, that sucks! -
Hussein's 1998 V70 Xr : The Force Awakens
Captain Bondo replied to lookforjoe's topic in Performance Modifications
The intent here is to get the car tuned. After that you can employ whatever electronic gizmo that you think will save you, provided it will interface with your given management system. I doubt the one you recommended will even interface into his existing system so it's irrelevant anyways. Also, if ambient temp swings make your car detonate, you suck at tuning. -
Hussein's 1998 V70 Xr : The Force Awakens
Captain Bondo replied to lookforjoe's topic in Performance Modifications
Or tune on the dyno using a set of det cans which are more accurate and cost about 10 bucks... -
Hussein's 1998 V70 Xr : The Force Awakens
Captain Bondo replied to lookforjoe's topic in Performance Modifications
Most mustang dynos allow for steady state/load holding operation. What you are suggesting is impossible though since heat management is an issue when tuning steady state, and you need to be able to control you fuel and ignition trim based on coolant and intake air temps. So not much point, since he can't. -
Hussein's 1998 V70 Xr : The Force Awakens
Captain Bondo replied to lookforjoe's topic in Performance Modifications
Cue broken record.... First of all, like you have been told countless times - do pulls with progressively increasing amounts of boost pressure. Do'nt just jump on there with 24psi or whatever insane amount and beat your head against the wall. Do a pull at 12psi. Adjust as needed. Then at 15psi. NOTE the differences! Then at 18, etc. How else are you going to tell where the system is at in terms of overall efficiency when you don't actually progress through the tuning in a systematic way? What does the car make at 12psi? Do you even know? Second of all, If I've said it once, I've said it 100 times. Until TT product a manual that actually describes how injector pulsewidth and spark advance are actually calculated, and what inputs affect them in what way, the system is next to useless. Blah blah yeah some people have made it work I know. Regardless, I would not feel dafe even trying to tune a system where I have no control over any of the secondary correction factors like IAT, or description of how they are calculated. It's tuning equivalent of "pin the tail on the donkey". Just put a blindfold on and wander around until you get where you want to be (and hope you don't pop too many motors on the way).... I know this doesn't really help you specifically, but I keep beating this drum in hopes that someone at TT will read it and actually do something. Mapping an engine management system (especially a plug'n'play) should take a few hours, not a few months. With these two issues working together, you are going to have a hard time making any power. -
Hussein's 1998 V70 Xr : The Force Awakens
Captain Bondo replied to lookforjoe's topic in Performance Modifications
So works how you want now? I dunno man the setup just seems so awkward and complex to me... one can with BIG filters, and a good baffle should do the job in a much simpler fashion. I am rough-tuning the new EMS this weekend and will start building my breather system this week - I'll make a thread maybe it will give you some more ideas. -
Hussein's 1998 V70 Xr : The Force Awakens
Captain Bondo replied to lookforjoe's topic in Performance Modifications
See this link, post 12. http://www.honda-tech.com/showthread.php?t=2740042 T1 race datalogged crankcase pressure on a race motor with a proper breather setup - 8600rpm and 44psi of boost. 0.1psi of crankcase pressure. You're venting to atmoshpere, therefore the crankcase pressure should be very close to atmosphere. You would benefit form more breather flow IMO. -
Hussein's 1998 V70 Xr : The Force Awakens
Captain Bondo replied to lookforjoe's topic in Performance Modifications
You have to baffle the openings in the cam cover, you can't just drill big holes and stick the fittings straight on, the cams will sling a crapton of oil into the lines... The "number" of an AN fitting is the size in 16s of an inch. -8 is 8/16" is 1/2" -
Hussein's 1998 V70 Xr : The Force Awakens
Captain Bondo replied to lookforjoe's topic in Performance Modifications
Like I keep saying. 2x -10 fittings as a minimum. That is 2 x 5/8" lines. Do it properly once rather than a dozen times. and flaco is totally right. whiteblocks seem to have crankcase pressure like whoa when you up the power. -
Hussein's 1998 V70 Xr : The Force Awakens
Captain Bondo replied to lookforjoe's topic in Performance Modifications
This is why I am saying you need a pair of -10an fittings coming off the head, in addition to the stock block breather port - open air works but you need lots of flow. No doubt using turbo vaccuum works with less hoses/fittings etc, but IMO re-introducing those low-octane hydrocarbons back into the motor is too big of a price to pay. Just my opinion. Glad this fixed it. -
Hussein's 1998 V70 Xr : The Force Awakens
Captain Bondo replied to lookforjoe's topic in Performance Modifications
Stick the end of the tube into a plastic coke bottle then. Do I have to think of everything? I've done it dozens of times on dozens of cars. I reckon I need 2 -10an breather fittings on the head. On the to-do this for this winter. -
Hussein's 1998 V70 Xr : The Force Awakens
Captain Bondo replied to lookforjoe's topic in Performance Modifications
So pull the dip stick, stick a draft tube on it, and see if you get less smoke. Takes like 5 minutes.... IMO the stock box is marginal at best for 7000rpm and 20+psi you probably need additional breathing, steel wool or not. -
Hussein's 1998 V70 Xr : The Force Awakens
Captain Bondo replied to lookforjoe's topic in Performance Modifications
Disagree. That, to me, suggests a crankcase breathing issue. Not a turbo issue. When you don't boost it up, you don't get as much blowby past the rings and have a fairly low amount of blowby gases entering the crankcase past the rings. When you boost it, the additional combusiton pressure forces gasses into the crankcase, then when you snap the throttle closed the crankcase pressure is driven up past the rings along with oil vapor. My car does the same thing and I have a dead straight -12 (3/4") drain line. I need a better breather setup. -
Hussein's 1998 V70 Xr : The Force Awakens
Captain Bondo replied to lookforjoe's topic in Performance Modifications
That turbine wheel looks more like the appropriate size. A TD05H turbine wheel has what, a 56mm major diameter? 56mm turbine major and 78mm compressor wheel is a bit of a mismatch.... You are supposed to keep the turbine wheel to within 80% of the diameter of the compressor wheel.... -
Hussein's 1998 V70 Xr : The Force Awakens
Captain Bondo replied to lookforjoe's topic in Performance Modifications
60-1 is a big compressor. Like 550whp. I wonder how big a td05 turbine shaft is compared to a T3 or T4... -
Hussein's 1998 V70 Xr : The Force Awakens
Captain Bondo replied to lookforjoe's topic in Performance Modifications
So if you turn the boost right down it stops smoking? That's some crazy wear. It seems like maybe the thrust loads on this turbo are just too high at your boost/flow rates or something. I mean every time it comes apart, it just looks pounded... I know it's a pain to re-do lines and downpipes and etc, and I know this is kinda lame advice - but before you spend money on more parts and a bigger compressor capable of putting even more load on the turbine shaft, is it possible that it's time to consider something like a Precision billet turbo that's built to withstand 25+psi on a constant basis? Again I hate to say that probably almost as much as you hate hearing it... but that's my thoughts...